A research team at the University of Washington has created a novel system that can measure platelet function within two minutes and can help doctors determine which trauma patients might need a blood transfusion upon being admitted to a hospital. The team published its results March 13 in Nature Communications. The microfluidics cards used in this study were made at WNF.
New method to assess platelet health could help ER doctors | UW News
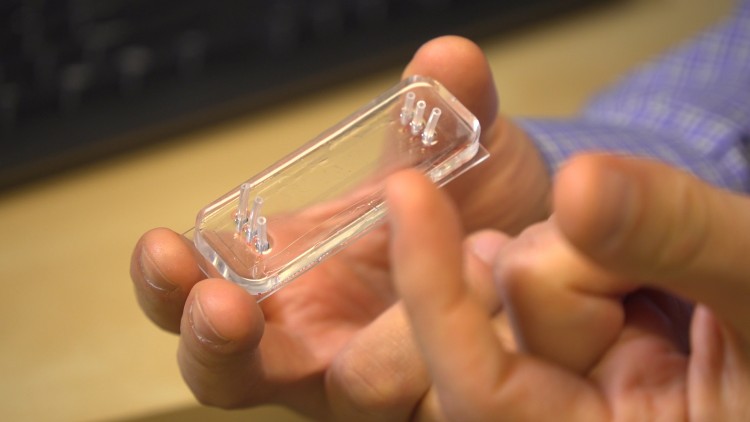